The field of electrical engineering is highly competitive. Landing your dream job requires more than just technical knowledge; it demands a strong understanding of core concepts and the ability to articulate them effectively in an interview setting. This article serves as your comprehensive guide to mastering electrical machines interview questions. We’ll delve deep into the fundamental principles, explore various machine types, and equip you with the knowledge and strategies needed to confidently navigate your interview and secure that coveted position.
Electrical Machines Interview Questions: Basic Concepts
Basic concepts like electromagnetic induction, magnetic circuits, and types of electrical machines will be tested.
1) What is an electrical machine? Explain the basic principle of operation.
An electrical machine is a device that converts energy. This conversion process can occur in two directions:
Electrical to Mechanical: This is the principle behind motors, which utilize electrical energy to generate mechanical force and motion. Examples include the motor in your electric fan or the traction motors propelling an electric train.
Mechanical to Electrical: This is the principle behind generators, which convert mechanical energy, often from a rotating shaft, into electrical energy. A hydroelectric dam, where the force of falling water spins turbines connected to generators, exemplifies this process.
The underlying principle governing these energy conversions is electromagnetic induction. This phenomenon, discovered by Michael Faraday, describes how a changing magnetic field induces an electromotive force (EMF), or voltage, within a conductor. This EMF, in turn, can drive a current, leading to the production of mechanical force (in a motor) or the generation of electrical power (in a generator).
2) Explain Faraday’s laws of electromagnetic induction and Lenz’s law.
Faraday’s Laws of Electromagnetic Induction are fundamental to understanding how electrical machines function. They can be summarized as follows:
First Law: When the magnetic flux linking a conductor changes, an EMF is induced in the conductor. The magnitude of this induced EMF is directly proportional to the rate of change of flux linkage.
Flux linkage refers to the product of the magnetic flux and the number of turns in the coil. A stronger magnetic field, more turns in the coil, or a faster change in the field will all result in a larger induced EMF.
Second Law: The direction of the induced EMF is such that it opposes the change that produced it. This law is a manifestation of the conservation of energy; it prevents the induced current from further strengthening the magnetic field and creating a runaway effect.
Lenz’s Law provides a concise way to determine the direction of the induced EMF. It states:
The induced EMF always acts in a direction that opposes the change in magnetic flux that caused it.
Imagine a magnet approaching a coil of wire. The approaching magnet increases the magnetic flux through the coil. According to Lenz’s law, the induced current in the coil will flow in a direction that creates a magnetic field opposing the magnet’s approach. This opposition helps to stabilize the system and prevent uncontrolled energy generation.
3) What are the different types of electrical machines?
Electrical machines are broadly categorized into two main types based on the type of current they utilize:
DC Machines: These machines operate on direct current (DC), where the current flows consistently in one direction. DC machines can function as both motors and generators. Examples include:
- DC motors: Used in applications requiring precise speed control, such as in electric vehicles and robotics.
- DC generators: Historically used for power generation, now often found in specialized applications like welding.
AC Machines: These machines operate on alternating current (AC), where the current periodically reverses direction. AC machines encompass a wider range of devices, including:
- Transformers: Used to increase or decrease the voltage of AC power, essential for efficient power transmission and distribution.
- Induction Motors: The most common type of AC motor, known for their simplicity and robustness. Found in a wide variety of applications, from household appliances to industrial machinery.
- Synchronous Motors: Run at a constant speed determined by the supply frequency. Used in applications requiring precise timing and speed control, such as clocks and industrial processes.
4) What is the difference between a motor and a generator?
While both motors and generators rely on the principle of electromagnetic induction, their functions are distinct:
Motor: A motor converts electrical energy into mechanical energy. It uses electrical power supplied to its windings to create a magnetic field that interacts with the rotor, producing rotational force (torque) and motion.
Generator: A generator converts mechanical energy into electrical energy. Mechanical energy, typically from a rotating shaft, drives the rotor within a magnetic field. This rotation induces an EMF in the stator windings, generating electrical power.
In essence, a motor consumes electrical energy to produce motion, while a generator utilizes motion to produce electrical energy.
5) Explain the concept of back EMF.
Back EMF (electromotive force) is a crucial concept in the operation of DC motors. It is a voltage that is generated within the motor itself as it rotates. This voltage opposes the applied voltage that drives the motor.
Here’s how it works:
When a DC motor rotates, its armature windings cut through the magnetic field produced by the stator.
According to Faraday’s law, this motion induces a voltage in the armature windings.
This induced voltage, known as back EMF, opposes the applied voltage according to Lenz’s law.
The magnitude of the back EMF is directly proportional to the motor’s speed. When the motor starts, the back EMF is low because the speed is low. As the motor accelerates, the back EMF increases. This has several important effects:
- Speed Regulation: Back EMF helps to regulate the motor’s speed. As the load on the motor increases, its speed tends to decrease. This decrease in speed reduces the back EMF, allowing more current to flow through the armature. The increased current provides more torque, helping the motor to maintain its speed.
- Current Limiting: Back EMF limits the current flowing through the armature. Without back EMF, the armature current would be very high, potentially damaging the motor windings.
6) What is the significance of synchronous speed?
Synchronous speed is a critical parameter in AC machines, particularly in induction and synchronous motors. It refers to the speed of the rotating magnetic field produced by the stator windings. This speed is determined by the following formula:
Synchronous Speed (Ns) = (120 * f) / P
where:
f is the frequency of the AC supply (in Hertz)
P is the number of poles in the stator winding
For example, a 4-pole motor connected to a 60 Hz supply will have a synchronous speed of:
Ns = (120 * 60) / 4 = 1800 RPM
Significance of Synchronous Speed:
Induction Motors: In an induction motor, the rotor always rotates at a speed slightly less than the synchronous speed. This difference in speed, known as slip, is essential for torque production. If the rotor were to rotate at synchronous speed, there would be no relative motion between the rotor and the rotating magnetic field, resulting in no induced current in the rotor and, consequently, no torque.
Synchronous Motors: In a synchronous motor, the rotor rotates at precisely the synchronous speed. This synchronous operation makes these motors suitable for applications where precise speed and timing are crucial, such as clocks, timers, and industrial processes requiring accurate synchronization.
7) Explain the concept of power factor in electrical machines.
Power factor is a measure of how effectively an AC electrical machine utilizes the power supplied to it. It represents the phase relationship between the voltage and current waveforms. In an ideal scenario, the voltage and current are in phase (power factor of 1), meaning that all the supplied power is used for doing useful work. However, in real-world applications, especially those involving inductive loads like motors and transformers, the current lags behind the voltage. This lag results in a power factor less than 1.
Why is power factor important?
Efficiency: A low power factor indicates that a portion of the supplied power is not being used for productive work. This wasted power, known as reactive power, circulates in the system, increasing losses and reducing overall efficiency.
Capacity: A low power factor requires a larger current to deliver the same amount of real power. This increased current can overload electrical systems, leading to higher energy costs and potential equipment damage.
Improving Power Factor:
To improve power factor, we typically add capacitors to the circuit. Capacitors provide a leading current that counteracts the lagging current caused by inductive loads. This brings the voltage and current waveforms closer to being in phase, increasing the power factor and improving the system’s efficiency.
Now, let’s explore the specific types of DC machines and their working principles.
Electrical Machines Interview Questions: DC Machines
DC machines are widely used in various applications. You may be asked about the working principle, types, characteristics, and applications of DC motors and generators.
8) Explain the construction and working principle of a DC motor.
A DC motor is a device that converts direct current (DC) electrical energy into mechanical energy in the form of rotation. Its construction consists of the following key components:
Stator: The stationary outer frame of the motor. It houses the field poles, which create the magnetic field necessary for motor operation. The field poles can be permanent magnets or electromagnets (field windings).
Rotor (Armature): The rotating part of the motor. It consists of an armature core, armature windings, and a commutator. The armature windings carry the current that interacts with the stator’s magnetic field to produce torque.
Commutator: A cylindrical arrangement of insulated copper segments mounted on the rotor shaft. The commutator acts as a mechanical switch, reversing the direction of current flow in the armature windings as the rotor rotates. This ensures continuous rotation by maintaining the correct magnetic force interaction.
Brushes: Made of carbon or graphite, brushes make contact with the commutator segments, providing a path for the current to flow to the armature windings.
Working Principle:
The operation of a DC motor is based on the interaction between the magnetic field produced by the stator and the current flowing through the armature windings.
- Magnetic Field: The stator’s field poles create a magnetic field.
- Current Flow: When DC current is supplied to the motor, it flows through the brushes to the commutator and then to the armature windings.
- Force and Torque: The current-carrying armature conductors experience a force within the magnetic field. This force, according to Fleming’s left-hand rule, acts perpendicular to both the magnetic field and the current direction. The force on the conductors creates a torque that causes the rotor to rotate.
- Commutation: As the rotor rotates, the commutator segments come into contact with different brushes, reversing the current direction in the armature windings. This commutation process ensures that the torque on the rotor remains in the same direction, resulting in continuous rotation.
9) What are the different types of DC motors? Explain their characteristics and applications.
DC motors are classified based on how their field windings are connected to the armature windings. This connection determines their characteristics and suitability for different applications.
Shunt Wound DC Motor:
Connection: The field winding is connected in parallel with the armature winding.
Characteristics:
- Relatively constant speed over a wide load range (good speed regulation).
- Low starting torque.
Applications: Suitable for applications requiring constant speed, such as:
- Fans
- Blowers
- Pumps
- Machine tools
Series Wound DC Motor:
Connection: The field winding is connected in series with the armature winding.
Characteristics:
- High starting torque.
- Speed varies significantly with load (poor speed regulation).
- Speed can become dangerously high at low loads.
Applications: Well-suited for applications requiring high starting torque and where speed regulation is not critical, such as:
- Traction motors in electric trains and locomotives
- Cranes
- Hoists
- Starter motors in automobiles
Compound Wound DC Motor:
Connection: Combines both series and shunt field windings.
Characteristics:
- Provides a balance of good starting torque and relatively constant speed.
Applications: Used in applications where both starting torque and speed regulation are important, such as:
- Elevators
- Conveyors
- Rolling mills
10) Explain the speed control methods for DC motors.
Controlling the speed of a DC motor is essential for various applications. Here are the common methods:
Armature Voltage Control:
Principle:The speed of a DC motor is directly proportional to the armature voltage. By varying the armature voltage, we can control the motor’s speed.
Methods:
- Rheostat: A variable resistor that controls the voltage applied to the armature. This method is simple but inefficient due to power losses in the rheostat.
- Pulse Width Modulation (PWM): A more modern and efficient technique where the voltage is switched on and off rapidly. The average voltage applied to the motor is controlled by varying the width of the on pulses.
Field Current Control:
- Principle: The speed of a DC motor is inversely proportional to the field flux. By varying the field current, we can change the field flux and, consequently, the motor’s speed.
- Method: A rheostat can be used to control the field current. This method is typically used for speed control above the base speed.
Solid-State Drives:
Principle: These electronic devices use sophisticated control algorithms and power electronics to provide precise and efficient speed control.
Advantages:
- Wide speed range
- High efficiency
- Improved performance
- Regenerative braking capabilities
11) What is an armature reaction? How does it affect the performance of a DC machine?
Armature reaction is a phenomenon that occurs in DC machines due to the interaction between the magnetic field produced by the armature current and the main magnetic field produced by the stator poles.
Effect: The armature current creates its own magnetic field that distorts the main magnetic field. This distortion can have several adverse effects on the machine’s performance:
- Reduced Torque: The distortion weakens the main magnetic field, reducing the torque produced by the motor.
- Sparking at Brushes: The shift in the magnetic field can cause sparking at the brushes, leading to increased wear and tear and potential damage to the commutator.
- Voltage Drop: Armature reaction can cause a voltage drop in the machine, reducing its efficiency.
Mitigation: To minimize the negative effects of armature reaction, several techniques are employed:
- Compensating Windings: These windings are embedded in the pole faces and carry a current that opposes the armature current, neutralizing its magnetic field.
- Interpoles: Small auxiliary poles placed between the main poles. They carry a current proportional to the armature current, creating a magnetic field that counteracts the distortion caused by armature reaction.
12) Explain the working of a DC generator.
A DC generator operates on the principle of electromagnetic induction to convert mechanical energy into DC electrical energy. Its construction is similar to a DC motor, with the key components being the stator, rotor (armature), commutator, and brushes.
Working Principle:
- Mechanical Rotation: The rotor is driven by an external mechanical source, such as a turbine or an engine.
- Induced EMF: As the armature windings rotate within the magnetic field produced by the stator poles, an EMF is induced in the windings according to Faraday’s law.
- Commutation: The commutator, in conjunction with the brushes, converts the induced alternating current (AC) in the armature windings into direct current (DC) at the output terminals.
- Output Voltage: The generated DC voltage is proportional to the speed of rotation and the strength of the magnetic field.
13) What are the different types of DC generators?
Similar to DC motors, DC generators are classified based on the connection of their field windings:
Shunt Wound DC Generator:
- Connection: The field winding is connected in parallel with the armature winding.
- Characteristics: Provides a relatively constant output voltage over a range of loads.
- Applications: Historically used for applications like battery charging and lighting.
Series Wound DC Generator:
- Connection: The field winding is connected in series with the armature winding.
- Characteristics: Output voltage varies significantly with load.
- Applications: Rarely used due to its unstable output voltage.
Compound Wound DC Generator:
- Connection: Combines both series and shunt field windings.
- Characteristics: Provides a stable output voltage with good load regulation.
- Applications: Used in applications requiring a constant voltage supply, such as welding machines.
Next, we will discuss AC machines, which are more prevalent in modern electrical systems.
Electrical Machines Interview Questions: AC Machines
AC machines are classified into synchronous and asynchronous machines. You may be asked about the working principle, types, and applications of these machines.
14) Explain the construction and working principle of a transformer.
A transformer is a static electrical machine that transfers electrical energy from one circuit to another through electromagnetic induction. It is used to increase or decrease the voltage of AC power without changing the frequency.
Construction:
- Core: Made of laminated ferromagnetic material, typically silicon steel, to reduce eddy current losses. The core provides a low reluctance path for the magnetic flux.
- Windings: Two or more coils of insulated copper wire wound around the core. The primary winding is connected to the input voltage source, and the secondary winding is connected to the load.
Working Principle:
- Primary Current: When AC voltage is applied to the primary winding, it creates a changing magnetic flux in the core.
- Induced EMF: This changing magnetic flux links with the secondary winding, inducing an EMF in it according to Faraday’s law.
- Voltage Transformation: The ratio of the number of turns in the primary winding to the number of turns in the secondary winding determines the voltage transformation ratio.
- Step-up transformer: More turns in the secondary winding, resulting in a higher output voltage.
- Step-down transformer: More turns in the primary winding, resulting in a lower output voltage.
15) What are the different types of transformers and their applications?
Transformers are categorized based on their function and application:
Step-up Transformer:
- Function: Increases the voltage level.
- Applications: Used in power plants to step up the generated voltage for efficient long-distance transmission.
Step-down Transformer:
- Function: Decreases the voltage level.
- Applications: Widely used in power distribution systems to reduce the high transmission voltage to a safe level for residential and commercial use.
Isolation Transformer:
- Function: Provides electrical isolation between the primary and secondary circuits. The primary and secondary windings are not electrically connected.
- Applications: Used for safety purposes in equipment where electrical isolation is crucial, such as medical devices and sensitive electronic equipment. It protects against electric shock and prevents ground loops.
Autotransformer:
- Function: A special type of transformer with a single winding that serves as both the primary and secondary winding. It is more efficient than traditional transformers for certain applications.
- Applications: Used for voltage regulation, starting induction motors, and in audio applications.
Current Transformer:
- Function: Used to measure large AC currents. It steps down the current to a lower level that can be safely measured by standard instruments.
- Applications: Widely used in power systems for metering and protection.
Potential Transformer:
- Function: Used to measure high AC voltages. It steps down the voltage to a lower level that can be safely measured.
- Applications: Used in power systems for metering and protection.
16) Explain the concept of transformer efficiency and losses.
Transformer efficiency is a measure of how effectively a transformer transfers electrical power from its primary winding to its secondary winding. It is expressed as the ratio of output power to input power. Transformers are known for their high efficiency, typically exceeding 95%. However, some energy losses occur during the transformation process:
Core Losses (Iron Losses):
- Hysteresis Loss: This loss occurs due to the repeated magnetization and demagnetization of the core material as the AC current alternates. The energy required to reorient the magnetic domains within the core is dissipated as heat.
- Eddy Current Loss: Eddy currents are circulating currents induced in the core material due to the changing magnetic flux. These currents generate heat, contributing to energy loss. To minimize eddy current losses, transformer cores are constructed from thin laminations of steel, which are electrically insulated from each other.
Copper Losses:
- I²R Losses: These losses occur due to the resistance of the copper conductors in the primary and secondary windings. The current flowing through the windings generates heat, proportional to the square of the current and the resistance of the wire.
Improving Transformer Efficiency:
Transformer manufacturers employ various techniques to minimize losses and improve efficiency:
- High-Grade Core Materials: Using high-quality core materials with low hysteresis and eddy current losses.
- Optimized Winding Design: Designing windings with low resistance to reduce copper losses.
- Proper Cooling: Employing effective cooling methods, such as oil immersion or forced air cooling, to dissipate heat generated by losses.
17) Explain the working principle of an induction motor.
An induction motor is a type of AC motor that operates on the principle of electromagnetic induction. It is widely used in various industrial and residential applications due to its simplicity, robustness, and low cost.
Construction:
- Stator: The stationary outer part of the motor. It houses the stator windings, which are connected to the AC power supply.
- Rotor: The rotating part of the motor. There are two main types of rotors:
- Squirrel Cage Rotor: The most common type, consisting of conductive bars embedded in a laminated iron core. The bars are short-circuited at their ends, forming a cage-like structure.
- Wound Rotor: Has windings on the rotor that are connected to external resistors through slip rings. This allows for external control of the motor’s characteristics.
Working Principle:
- Rotating Magnetic Field: When AC power is applied to the stator windings, it creates a rotating magnetic field in the air gap between the stator and rotor.
- Induced Current: This rotating magnetic field cuts through the rotor conductors, inducing an EMF and current in them according to Faraday’s law.
- Torque Production: The interaction between the rotating magnetic field and the induced rotor current produces a torque that causes the rotor to rotate.
- Slip: The rotor always rotates at a speed slightly less than the synchronous speed of the rotating magnetic field. This difference in speed, known as slip, is essential for the induction motor to produce torque.
18) What are the different types of induction motors?
Squirrel Cage Induction Motor:
- Construction: Simple and rugged rotor design with conductive bars embedded in a laminated core.
- Characteristics: Low cost, reliable, and requires minimal maintenance.
- Applications: Widely used in various applications, including fans, pumps, conveyors, and general-purpose industrial drives.
Wound Rotor Induction Motor:
- Construction: More complex rotor with windings connected to external resistors through slip rings.
- Characteristics: Provides higher starting torque and allows for speed control by varying the external resistance.
- Applications: Used in applications requiring high starting torque or where speed control is necessary, such as cranes, hoists, and elevators.
19) Explain the concept of slip in an induction motor.
Slip is a crucial concept in the operation of an induction motor. It refers to the difference between the synchronous speed (Ns) of the rotating magnetic field and the actual rotor speed (Nr). It is expressed as a percentage of synchronous speed:
Slip (s) = [(Ns – Nr) / Ns] * 100%
Significance of Slip:
- Torque Production: Slip is necessary for an induction motor to produce torque. If the rotor were to rotate at synchronous speed (s = 0), there would be no relative motion between the rotor conductors and the rotating magnetic field, resulting in no induced current and, consequently, no torque.
- Speed Regulation: The slip increases as the load on the motor increases. This increase in slip allows more current to be induced in the rotor, providing the necessary torque to handle the increased load.
Typical Slip Values:
- The slip of an induction motor typically ranges from 2% to 5% at full load. Higher slip values indicate lower efficiency.
20) What are the starting methods for induction motors?
Induction motors draw a high current when started directly on line (DOL). This high starting current can cause voltage dips in the power supply and may damage the motor windings. To mitigate this, various starting methods are employed:
Direct-on-line (DOL) Starting:
- Method: The simplest method, where the motor is connected directly to the full supply voltage.
- Suitable for: Small motors with low inertia loads.
Star-Delta Starting:
- Method: The motor windings are initially connected in a star configuration, which reduces the starting current. Once the motor reaches a certain speed, the connection is switched to delta for normal operation.
- Advantages: Reduces starting current by a factor of three.
- Suitable for: Medium-sized motors where reduced starting current is required.
Autotransformer Starting:
- Method: An autotransformer is used to reduce the voltage applied to the motor during starting. Once the motor reaches a certain speed, the autotransformer is bypassed, and the motor is connected to the full supply voltage.
- Advantages: Provides a smooth and controlled start with reduced starting current.
- Suitable for: Large motors where a gradual start is required.
Soft Starters:
- Method: These electronic devices use thyristors or other semiconductor switches to gradually increase the voltage applied to the motor during starting.
- Advantages: Provides smooth acceleration, reduced starting current, and adjustable starting parameters.
- Suitable for: Applications where precise control of starting characteristics is required.
21) Explain the working principle of a synchronous motor.
A synchronous motor is a type of AC motor that operates at a constant speed determined by the frequency of the power supply. Its rotor rotates in synchronization with the rotating magnetic field produced by the stator.
Construction:
- Stator: Similar to an induction motor, the stator houses the windings that create the rotating magnetic field.
- Rotor: The rotor has a DC supply that creates a magnetic field. This can be achieved using permanent magnets or a DC excitation winding.
Working Principle:
- Rotating Magnetic Field: The stator windings produce a rotating magnetic field when connected to an AC supply.
- DC Excitation: The rotor is provided with a DC excitation, creating a magnetic field on the rotor.
- Synchronization: The rotor’s magnetic field “locks onto” the rotating stator field, causing the rotor to rotate at the same speed as the rotating field.
22) What are the applications of synchronous motors?
Synchronous motors are used in applications where constant speed and high efficiency are required:
- Power Factor Correction: Synchronous motors can be operated at leading power factor, which helps to improve the power factor of an electrical system. This reduces reactive power and improves overall efficiency.
- Large Industrial Drives: Synchronous motors are used in large industrial applications, such as pumps, compressors, and mills, where constant speed and high efficiency are crucial.
- Precision Applications: Due to their precise speed control, synchronous motors are used in applications requiring accurate timing, such as clocks and timing devices.
23) Explain the concept of synchronous reactance.
Synchronous reactance (Xs) is an important parameter in synchronous machines. It represents the reactance of the armature winding when the machine is operating at synchronous speed.
Influence on Performance:
- Voltage Regulation: Synchronous reactance affects the voltage regulation of a synchronous generator. A higher synchronous reactance leads to poorer voltage regulation.
- Stability: Synchronous reactance also influences the stability of a synchronous motor. A higher synchronous reactance can make the motor more prone to oscillations and instability.
Synchronous reactance is determined by the physical construction of the machine, including the number of turns in the armature winding, the air gap length, and the magnetic properties of the core material.
Besides standard machines, there are special types of machines designed for specific applications.
Electrical Machines Interview Questions: Special Machines
Special machines like single-phase motors, universal motors, and stepper motors have unique characteristics and applications.
24) What are special machines? Give some examples.
Special machines are electrical machines designed for specific tasks or applications that require unique characteristics or functionalities. They often deviate from the conventional design of standard motors and generators. Some examples include:
- Stepper Motors: Rotate in discrete steps, providing precise positioning control.
- Servo Motors: Closed-loop control systems that provide accurate speed and position control.
- Linear Motors: Produce linear motion instead of rotary motion.
- Reluctance Motors: Operate based on the principle of magnetic reluctance.
- Brushless DC Motors: DC motors without brushes, offering high efficiency and long life.
25) Explain the working principle of a stepper motor.
A stepper motor is a brushless DC motor that rotates in discrete steps. It is widely used in applications requiring precise positioning and control.
Construction:
- Stator: The stator has multiple windings arranged in phases.
- Rotor: The rotor can be a permanent magnet or a variable reluctance type.
Working Principle:
- Sequential Energization: The stator windings are energized in a specific sequence, creating a rotating magnetic field.
- Stepwise Rotation: The rotor’s magnetic field aligns with the rotating stator field, causing the rotor to rotate in steps.
- Step Angle: The angle of rotation per step is determined by the number of phases and the number of poles in the motor.
26) What are the applications of stepper motors?
Stepper motors are used in a wide range of applications where precise positioning is required:
- CNC Machines: Controlling the movement of tools and workpieces in computer numerical control (CNC) machines.
- Printers: Precisely positioning the print head in printers and plotters.
- Robotics: Controlling the movement of robot arms and joints.
- Automotive: Used in automotive applications for throttle control, fuel injection, and mirror positioning.
- Medical Equipment: Used in medical devices for precise fluid dispensing and positioning of instruments.
27) Explain the working principle of a servo motor.
A servo motor is a closed-loop control system that uses feedback to achieve precise position and speed control. It typically consists of a motor, a position sensor (encoder or resolver), and a control circuit.
Working Principle:
- Command Signal: The control circuit receives a command signal specifying the desired position or speed.
- Feedback: The position sensor provides feedback to the control circuit about the motor’s actual position.
- Error Signal: The control circuit compares the desired position with the actual position and generates an error signal.
- Motor Control: The error signal is used to adjust the motor’s speed and direction to minimize the error and achieve the desired position.
Applications of Servo Motors:
Servo motors are used in applications requiring precise and dynamic control, such as:
- Robotics: Precise control of robot arm movements.
- CNC Machines: Accurate positioning of tools and workpieces.
- Automation Systems: Controlling actuators and positioning systems.
- Aerospace: Controlling flight surfaces and actuators in aircraft.
To effectively use electrical machines, it’s important to understand their applications and troubleshooting techniques.
Electrical Machines Interview Questions: Applications & Troubleshooting
You may be asked about the applications of different types of electrical machines in various industries. Additionally, you may be asked to troubleshoot common faults in electrical machines.
28) What are some common applications of electrical machines in industry?
Electrical machines play a vital role in various industrial sectors, powering a wide range of equipment and processes:
Manufacturing:
- Material Handling: Conveyor belts, cranes, hoists, and robotic arms for moving materials and products.
- Machine Tools: Lathes, milling machines, and grinders for shaping and cutting materials.
- Pumps and Compressors: For moving fluids and gases in various industrial processes.
Transportation:
- Electric Vehicles: Traction motors for propelling electric cars, buses, and trains.
- Aircraft: Electric motors for operating flight control surfaces, landing gear, and other systems.
Energy:
- Power Generation: Generators in power plants for converting mechanical energy into electrical energy.
- Renewable Energy: Wind turbines and hydroelectric generators for harnessing renewable energy sources.
HVAC (Heating, Ventilation, and Air Conditioning):
- Fans and Blowers: For circulating air in ventilation and air conditioning systems.
- Compressors: For compressing refrigerants in air conditioning and refrigeration systems.
29) How do you troubleshoot a faulty electrical motor?
Troubleshooting a faulty electrical motor involves a systematic approach to identify the root cause of the problem. Here are some common steps:
Visual Inspection:
- Physical Damage: Check for any visible signs of damage, such as burnt windings, loose connections, or damaged bearings.
- Overheating: Look for signs of overheating, such as discoloration of the windings or excessive heat radiating from the motor.
Testing:
- Insulation Resistance: Use a megohmmeter (insulation tester) to measure the insulation resistance between the windings and the motor frame. Low insulation resistance indicates a potential short circuit.
- Winding Resistance: Use a multimeter to measure the resistance of the motor windings. Abnormal resistance values can indicate an open circuit or a short circuit in the windings.
- Current Draw: Measure the current drawn by the motor using a clamp meter. Excessive current draw can indicate an overload or a fault within the motor.
Analyzing:
- Test Results: Analyze the test results to identify the possible cause of the fault.
- Operating Conditions: Consider the operating conditions of the motor, such as load, voltage supply, and environmental factors.
- Maintenance History: Review the motor’s maintenance history to identify any recurring problems or potential issues.
30) What are some common causes of motor failure?
Motor failures can occur due to various reasons, including:
Overheating:
- Overload: Operating the motor beyond its rated capacity can cause overheating.
- Poor Ventilation: Inadequate cooling can lead to heat buildup and damage to the motor windings.
- Faulty Bearings: Worn or damaged bearings can cause friction and excessive heat.
- Voltage Imbalance: An imbalance in the three-phase supply voltage can cause overheating and damage to the motor windings.
Bearing Failure: Bearing failure can result from wear and tear, lack of lubrication, or contamination.
Moisture and Contamination: Moisture ingress or contamination can cause insulation breakdown and short circuits in the motor windings.
Power Quality Issues: Voltage surges, transients, and harmonics in the power supply can damage the motor’s insulation and electronic components.
31) How can you improve the efficiency of an electrical machine?
Improving the efficiency of electrical machines is crucial for reducing energy consumption and operating costs. Here are some strategies:
- Proper Sizing: Select the right size motor for the application. Oversized motors operate at lower efficiency.
- Regular Maintenance: Regularly inspect and maintain the motor, including cleaning, lubrication, and checking for wear and tear.
- High-Efficiency Motors: Use high-efficiency motors designed to minimize losses. Look for motors with high efficiency ratings, such as IE3 or IE4.
- Power Factor Correction: Improve the power factor of the electrical system by adding capacitors to compensate for the lagging current caused by inductive loads like motors.
- Variable Speed Drives (VSDs): Use VSDs to optimize motor speed based on the load requirements. VSDs can significantly reduce energy consumption in applications with variable load demands.
- Reduce Friction: Minimize friction losses in bearings and other moving parts through proper lubrication and maintenance.
- Optimize Cooling: Ensure adequate cooling of the motor to prevent overheating. This may involve improving ventilation or using more efficient cooling methods.
To ace your electrical machines interview, follow these preparation tips and strategies.
Electrical Machines Interview Preparation Tips & Strategies
To prepare effectively, practice solving numerical problems, understand the underlying principles, and review the latest advancements in electrical machines.
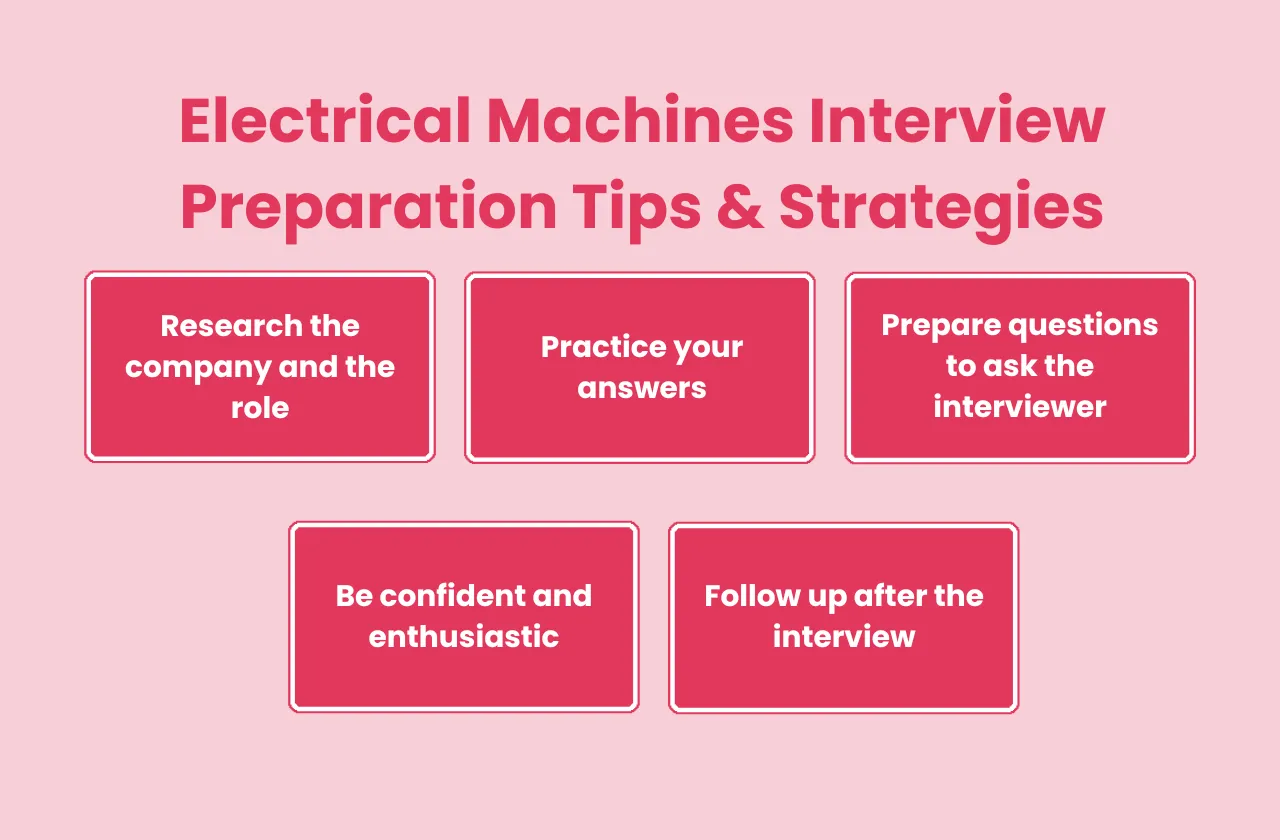
1) Research the company and the role.
Thorough research is essential before any job interview. For an electrical machines position, focus on:
Company’s Products and Services: Understand the company’s core business, the types of electrical machines they use, and the specific applications they serve. This will help you tailor your answers to their needs and demonstrate your relevance to their operations.
Industry Trends: Stay updated on the latest trends in electrical machine technology, such as advancements in motor efficiency, power electronics, and control systems.
Company Culture: Research the company’s values, mission, and work environment. This will help you assess your fit within the organization and prepare questions about their culture.
2) Practice your answers.
Practice makes perfect, especially when it comes to technical interviews. Here’s how to practice effectively:
Common Interview Questions: Prepare for common electrical machines interview questions, such as those covered in this article. Understand the underlying concepts and practice explaining them clearly and concisely.
STAR Method: Use the STAR method (Situation, Task, Action, Result) to structure your answers to behavioral questions. This method helps you provide specific examples of your skills and experience.
Mock Interviews: Conduct mock interviews with friends, family, or mentors to simulate the interview environment and get feedback on your performance.
Online Resources: Utilize online resources like iScalePro to practice with realistic interview questions and scenarios. These platforms often provide feedback on your responses and help you identify areas for improvement.
3) Prepare questions to ask the interviewer.
Asking insightful questions demonstrates your interest in the position and the company. Prepare a few questions beforehand, but be flexible and adapt to the flow of the conversation. Here are some examples:
Technical Questions:
- “What types of electrical machines are commonly used in your company?”
- “What are some of the challenges you face in maintaining and optimizing motor performance?”
- “Are there opportunities to work with new motor technologies or control systems?”
Role-Specific Questions:
- “Can you describe a typical day in this role?”
- “What are the key performance indicators for this position?”
- “What are the opportunities for professional development and growth within the company?”
Company Culture Questions:
- “How would you describe the company’s work environment and culture?”
- “What are the company’s values and how are they reflected in the day-to-day work?”
4) Be confident and enthusiastic.
Projecting confidence and enthusiasm is crucial in making a positive impression.
Body Language: Maintain good posture, make eye contact, and use hand gestures to emphasize your points.
Communication: Speak clearly and concisely, using technical terms accurately. Be passionate about your skills and experience.
Positive Attitude: Express your enthusiasm for the opportunity and your eagerness to contribute to the company.
5) Follow up after the interview.
Following up after the interview is a professional courtesy and reinforces your interest in the position.
Thank-You Note: Send a thank-you email to the interviewer within 24 hours. Express your gratitude for their time and reiterate your interest in the role.
Reiterate Key Points: Briefly mention key points from the interview and highlight your qualifications.
Inquiry: If you haven’t heard back within the timeframe discussed, you can send a follow-up email to inquire about the status of the hiring process.
By following these tips and strategies, you can confidently face your electrical machines interview.
Conclusion
This comprehensive guide has equipped you with the knowledge and strategies needed to excel in your electrical machines interview. By mastering the fundamental concepts, understanding various machine types, and practicing your responses, you can confidently showcase your expertise and secure your desired position. Remember to research the company, prepare insightful questions, and project confidence and enthusiasm throughout the interview process. With thorough preparation and a positive attitude, you can successfully navigate your interview and embark on a rewarding career in the field of electrical machines.
Electrical Machines Interview FAQs
1) What are the basics of electrical machines?
Electrical machines convert energy between electrical and mechanical forms. They use electromagnetic principles to achieve this. Key concepts include magnetic fields, electromagnetic induction, and forces generated by current-carrying conductors in magnetic fields.
2) What are the three main types of electrical machines?
The three main types of electrical machines are:
- Motors: Convert electrical energy into mechanical energy (rotation). Examples include fans, pumps, and electric vehicles. Â
- Generators: Convert mechanical energy into electrical energy. Examples include wind turbines and hydroelectric power plants. Â
- Transformers: Change the voltage of an alternating current (AC) supply. They are essential for power transmission and distribution. Â
3) How do I prepare for an electrical interview?
To prepare for an electrical interview:
- Review fundamental concepts: Study electrical engineering principles, laws, and formulas (Ohm’s Law, Kirchhoff’s Laws, etc.). Â
- Practice common interview questions: Research and prepare answers to frequently asked questions about electrical machines, power systems, and troubleshooting.
- Gain practical experience: Internships, projects, and relevant work experience provide valuable hands-on knowledge and demonstrate your skills. Â
- Improve communication skills: Practice explaining technical concepts clearly and concisely. Â
4) What is the principle of an electrical machine?
The principle of an electrical machine is based on the interaction between magnetic fields and electric currents.
- Motors operate by passing a current through a conductor placed in a magnetic field. This creates a force that causes the conductor to rotate. Â
- Generators work in reverse. When a conductor moves through a magnetic field, an electromotive force (voltage) is induced in the conductor. Â
- Transformers utilize the principle of electromagnetic induction to transfer energy between two or more circuits with different voltage levels. Â